About Us
Our Mission Statement:
At Flight Systems Inc., we are committed to delivering top tier Printed Circuit Board Assemblies for the power generation industry, built to the highest production standards. We believe that excellence in quality goes hand in hand with responsibility, which is why we prioritize both precision in our products and fairness in our workplace. By paying all our employees a living wage, we foster a culture of respect, innovation, and sustainability, ensuring that our values are reflected in every product we create.Our Quality Policy:
Flight Systems Inc. is dedicated to delivering high-quality printed circuit board assemblies, meeting the highest standards and regulatory requirements. We foster a culture of continuous improvement, focusing on enhancing processes, customer satisfaction, and operational efficiency. Quality is a shared responsibility among all employees, and we work together to improve our products and services. Through innovation and collaboration, we aim to exceed customer expectations in every aspect of our business.Our Quality Objectives:
-
Compliance with Requirements
- We strictly adhere to ISO-9001:2015 standards, industry regulations, and all customer-specific requirements, ensuring that every product meets stringent quality criteria.
- Improve customer satisfaction by addressing complaints promptly, ensuring on-time deliveries, reducing warranty claims, and enhancing product quality through corrective actions and process improvements.
- Reduce product defects and rework, ensuring products meet quality standards on the first inspection.
- Streamline manufacturing processes and reduce waste, leading to increased operational efficiency.
- Ensure that all employees are fully trained in the quality management system to enhance efficiency, reduce errors, and foster a culture of continuous improvement.
Enhance Customer Satisfaction
Increase Product Reliability and Reduce Waste
Implement Comprehensive Employee Training Programs
Here is a glimpse into our production process:
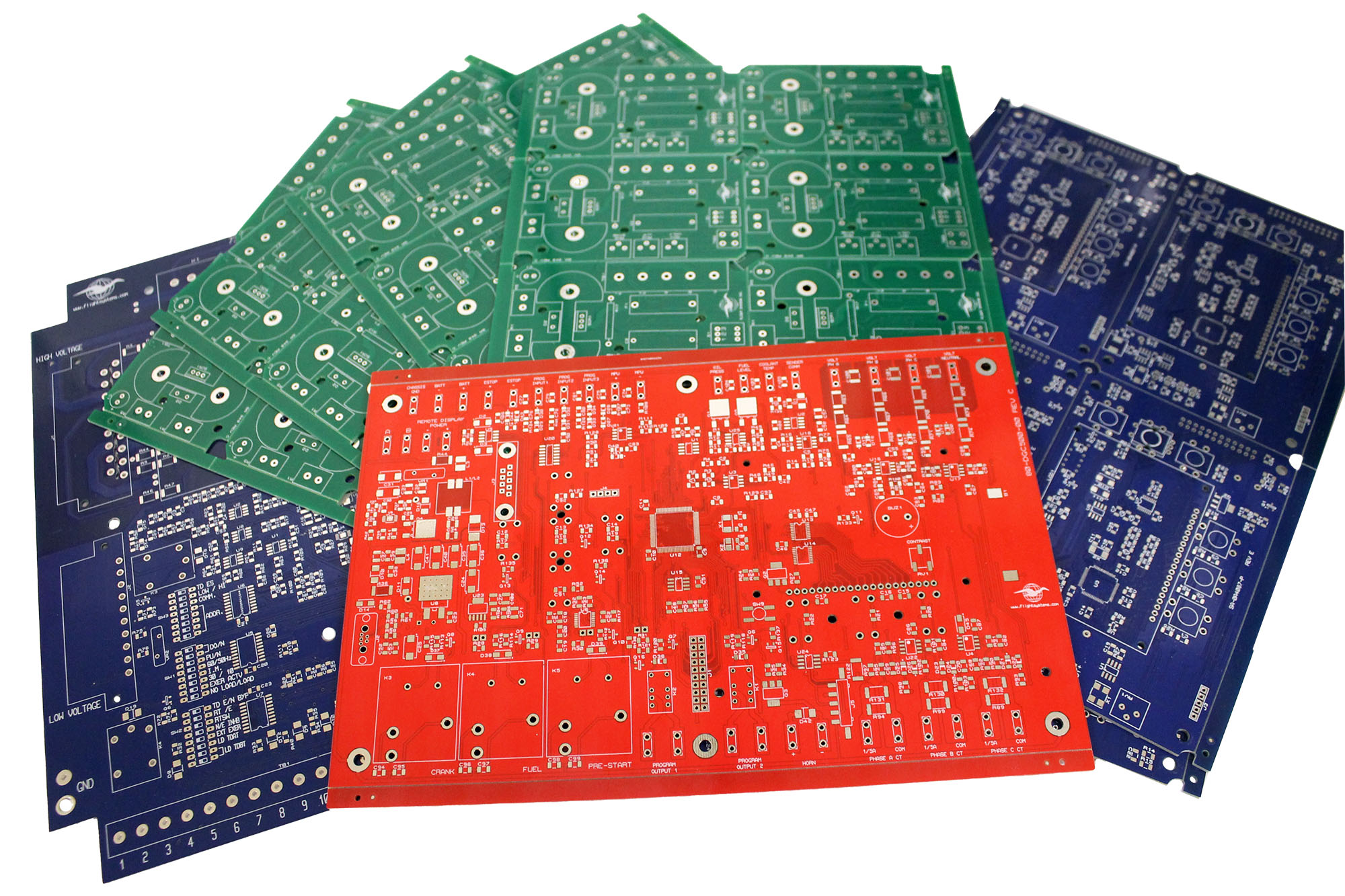
Circuit Boards
The assembly of our products starts with a blank circuit board. We purchase high quality circuit boards, cut to size, with our design layout already etched. All other assembly is done in-house by Flight Systems.Pasting
Blank boards that require surface mount components are first routed through our pasting process. Pasting is done by squeezing solder paste through a stencil that contains cutouts for all of the pads that need solder applied. The machine pictured here aligns the stencil to the board to be pasted using very accurate cameras. Once the marks are aligned, a squeegee spreads the solder paste over the stencil. This allows for accurate, repeatable results every time. We can virtually eliminiate solder bridging between components this way.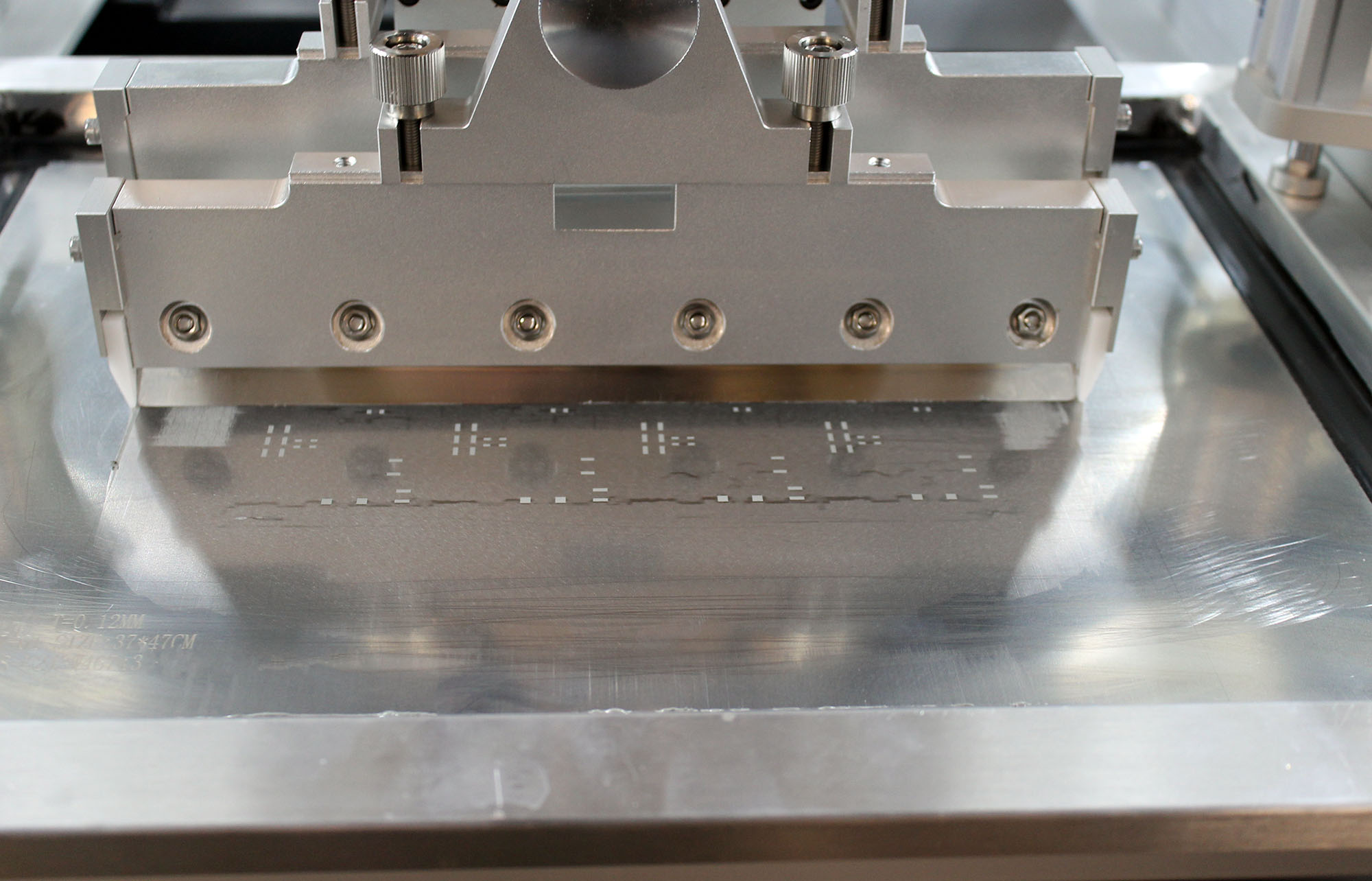
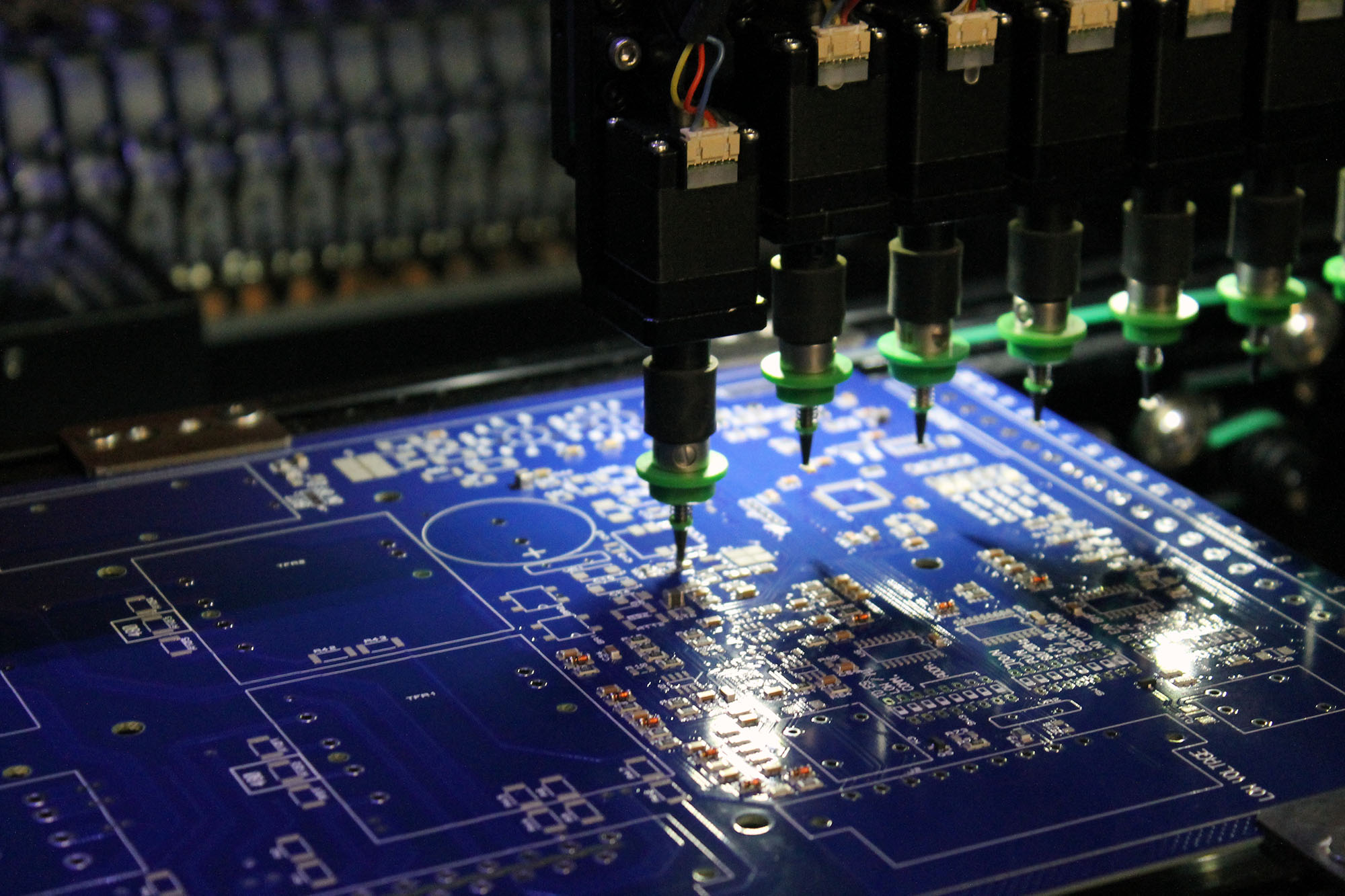
SMT Placer
Once a board has been pasted, it transitions to the surface mount placer. This machine takes components from reels and picks them up using an array of vacuum nozzles. Each part is scanned by a camera and rotated to line up with the pads that it belongs on. Again, in this step, accuracy is the key. As each board passes through the series of machines, each surface mount component is placed, until the board is fully populated. Any surface mount components that can not be placed using the machine will be placed by a technician using tweezers. At this stage, the board is inspected for any misplaced or shifted parts. The board is then run through a conveyor style oven. This step causes the solder paste to liquefy and connect the part to the board. During the journey through the oven, the temperature is highly controlled. This allows for a properly flowed solder joint without heat-damaging the components.Selective Solder
Most boards will also require through-hole components, such as connectors, relays, and various other parts. These boards are run through our selective solder process. Through-hole component leads are trimmed to a specific size and then loaded into the board. The board is then placed into a selective solder machine. This machine passes a fountain of solder underneath the board along a programmed path to solder the components to the board. Rather than a wave soldering process that will touch the entire underside of the board, selective solder allows more control over soldering points. This, in turn, allows better temperature control of the circuit board and parts.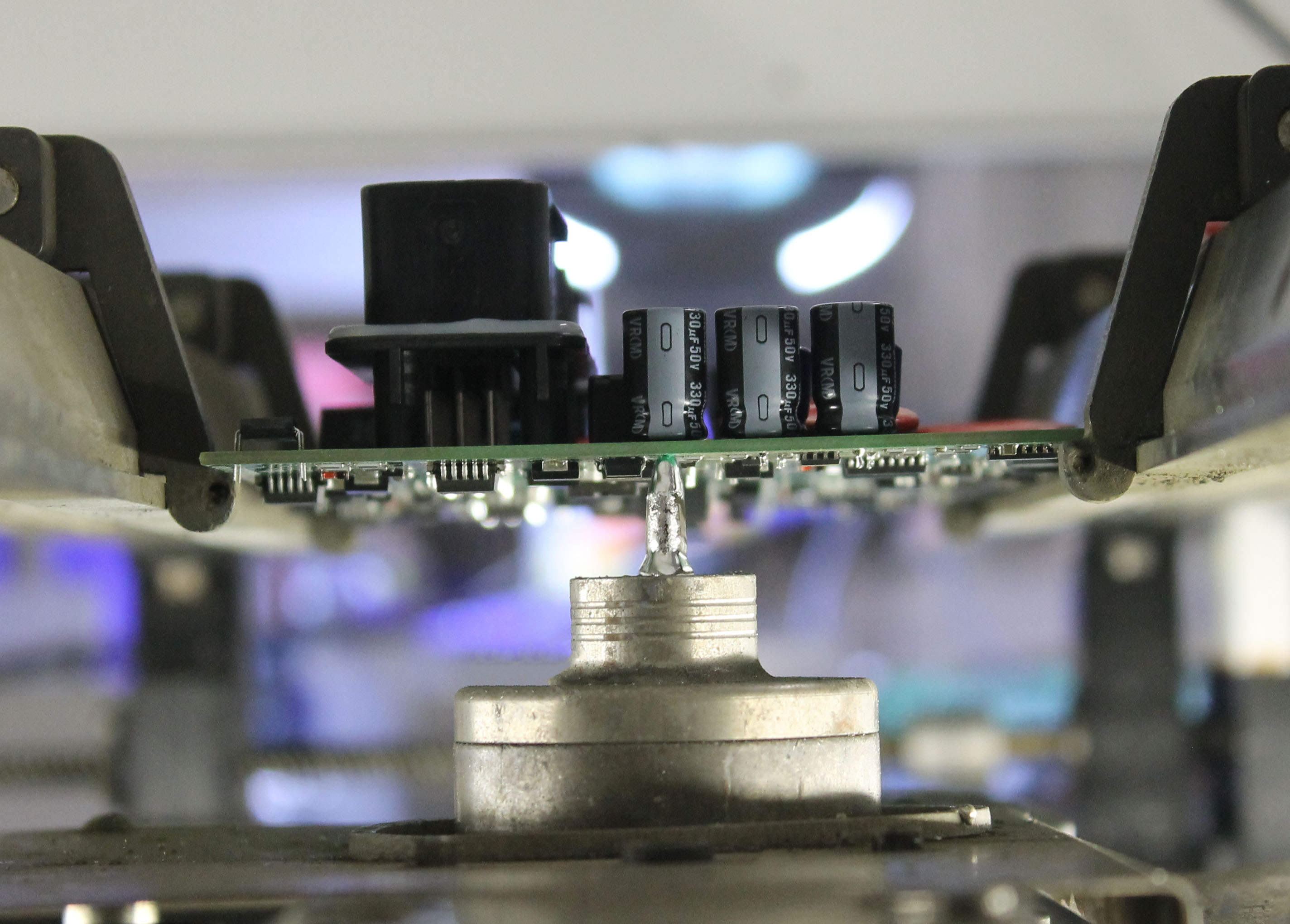
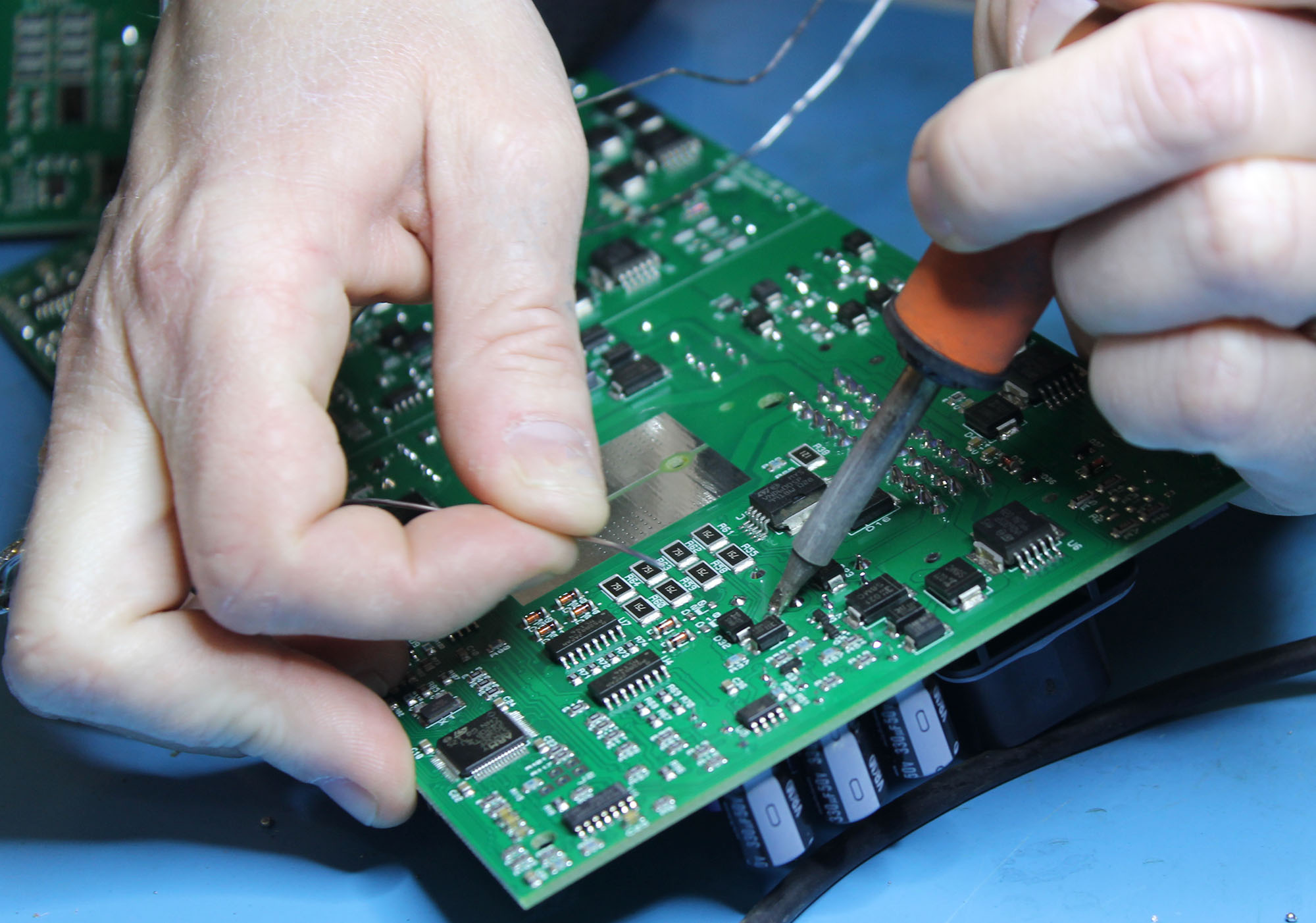
Hand Production
Some boards will also need larger components, such as transformers, assembled by hand. During this step, the production team will solder the parts to the board using a soldering iron. After all soldering is done, each board will be inspected and tested.Testing
All boards and controllers produced by Flight Systems go through extensive testing before and after they are coated or encapsulated. This ensures initial functionality as well as continued functionality after the coating or encapsulation has flowed between and under parts. All of our test equipment is built in-house by our engineers. This allows full control over how boards get tested. All functions of the board are tested using a mock-up of the equipment that the product will be installed on.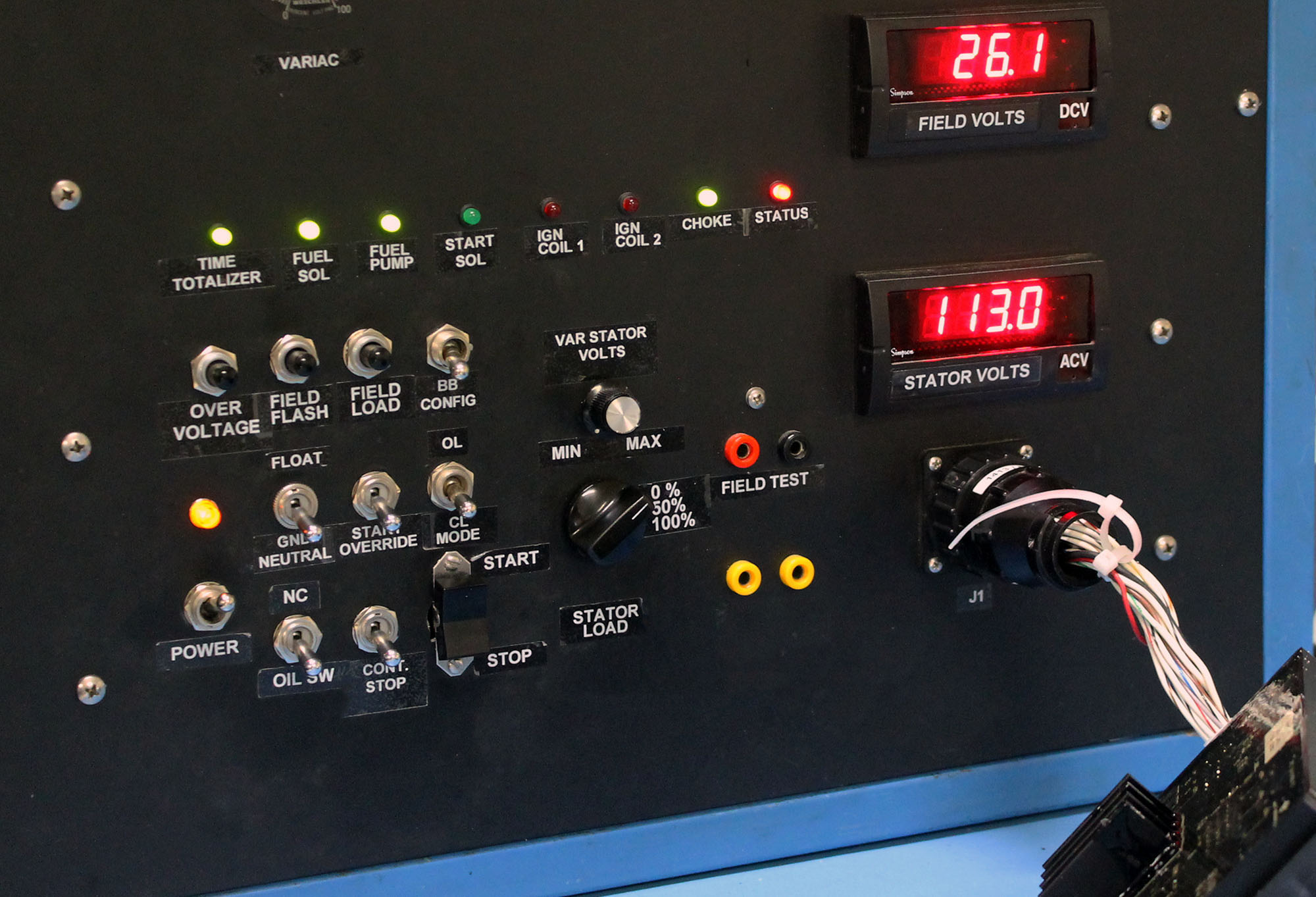
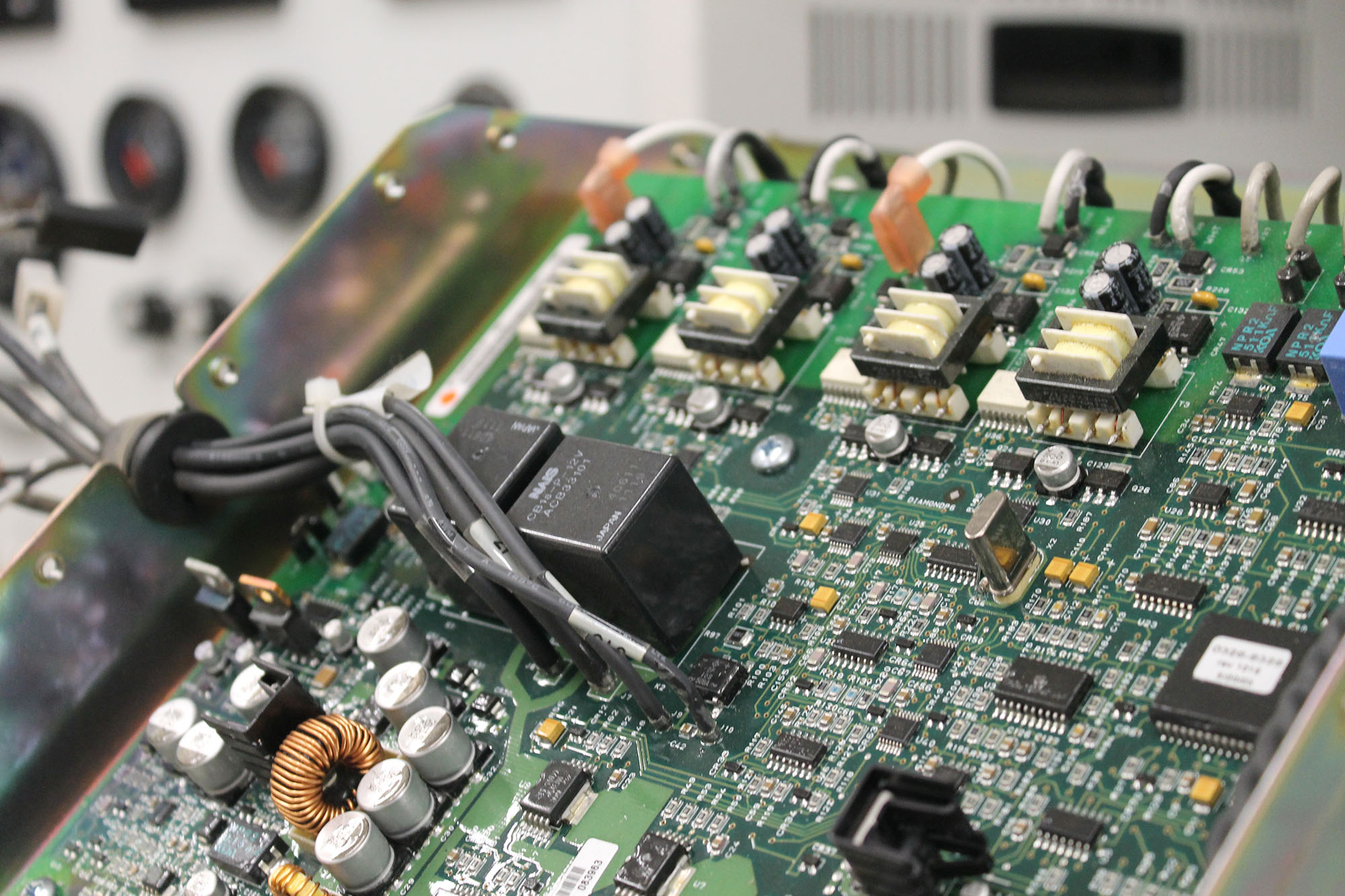
Repair
Our repair department troubleshoots and repairs many manufacturer's controllers and boards. Our repairs cost a fraction of what board replacement may cost. Many customers utilize our repair services to keep their obsolete controls in service. Without our repair capabilities, many generators would need to be completely replaced due to obsolete control systems.Flight Systems started over 50 years ago developing and producing then "state-of-the-art" electronic controls used in the aerospace program.
Our equipment flew aboard Apollo 11 when Neil Armstrong was the first man to set foot on the moon, Apollo 17 with Gene Cernan and the Lunar Rover, and several later Skylab missions.
1970 – Launched forklift solid state control services and spare parts, now a separate organization – FSIP Electronics |
1972 – Received Fairchild Quality Award for Skylab |
1973 – Received U.S. Government Defense Electronics Award for Quality and On-Time Deliver |
1978 – Began servicing generator controls for dealers servicing Publix and Winn Dixie supermarkets |
1980 – First installation of the Engine Saver® in Palabora mines in South Africa |
1982 – Began servicing automotive electronics - now a separate organization - Dorman Products |
1985 – Earned American Bureau of Shipping (ABS) Certification for the Engine Saver.® |
1988 – Received a contract to remanufacture Chrysler vehicle electronics |
1991 – Received the first of seven Chrysler Outstanding Supplier Awards for quality and delivery. |
1993 – Received U.S. General Services Administration approval for our generator regulator controls |
1997 – Earned QS-9000 Quality Certification |
2002 – Earned ISO14001 Environmental Certification |
2003 – Earned TS16949 World Standard for Quality Certification |
2013 – Moved operations from Lewisberry, PA to Mechanicsburg, PA, allowing us to expand our manufacturing and repair service capabilities. |
2018 – 50th anniversary of Flight Systems Inc. |
2025 – Earned ISO 9001:2015 Quality Certification |
For over 30 years, we have supplied new replacement parts and rebuilt electronic controls for all types of gen sets. That includes regulators, start/stop controls, automatic switching controllers and engine monitors. We are the largest and longest established independent rebuilders of Generator Controls and we are proud of it.
For over 40 years, we supplied controls that protected engines by detecting problems caused by oversight, abuse, neglect, overwork and normal wear & tear. Our Engine Saver© has many hundreds of satisfied users who have saved thousands – in some cases hundreds of thousands of dollars – because the Engine Saver did its job and prevented a small developing problem from causing consequential engine damage and lost productivity.

In Memory of Bob Shaffner
Chairman/CEO 1937 - 2012
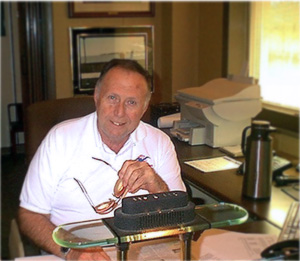
In 1968 Bob Shaffner and Robert York co-founded Flight Systems Inc. in Mechanicsburg, PA. The companys earliest products included communications relays, and as an approved NASA supplier Flight Systems equipment flew on the Apollo and Skylab missions.
Throughout the years, Flight Systems has ventured into many areas of electronic controls including those used in forklifts and other electric vehicles, generators, and monitoring/protection for industrial and marine diesel engines. Other successful ventures over the years include an architectural steel fabricating company and cable TV and internet service.
